Specification considerations
Choosing the correct grease trap is essential to prevent problems and product failures. The materials of the trap, regulations, access and maintenance and installation all impact product selection.
Construction materials
Various materials are used to manufacture grease traps that will affect the performance and design life of the product.
ACO Passavant grease traps are manufactured from lightweight polyethylene assisting workplace health and safety.
For more detailed information, click here.
Regulations
There are local and international regulations that govern the specification of below and above ground grease traps.
Below ground grease traps require access covers for maintenance and must comply with load class regulations.
For more detailed information, click here.
Access for maintenance
Grease traps need to be serviceable.
ACO’s range of grease traps have dedicated access points for regular servicing and maintenance. ACO’s Lipumax below ground grease traps have the advantage of a single access point.
For more detailed information, click here.
Buoyancy
Buoyancy in high water table areas must be considered at the specification stage for below ground grease traps to prevent uplift.
ACO’s Lipumax grease traps are specifically engineered for below ground installations.
For more detailed information, click here.
The material chosen for the grease trap will affect its durability and design life. The most common materials used for the manufacture of grease traps are described below.
EcoJet and Lipumax-P grease traps are manufactured from rotational moulded polyethylene. Polyethylene is a lightweight, flexible and robust material that facilitates handling and installation.
Polyethylene is durable and has excellent chemical and corrosion resistance properties. Polyethylene does not require re-lining and is suitable for installations in acidic and alkaline soils.
Polyethylene is significantly more impervious than other materials, ensuring no leaching of wastewater which is a requirement when installed in sensitive environments.
Precast concrete grease traps have thick walls to provide structural integrity. They are heavy, cumbersome and difficult to transport requiring higher installation costs as cranes and specialist equipment are needed to excavate and install the grease trap.
Cement concrete is a porous material and can absorb water up to 3% by weight. Concrete grease traps require regular maintenance and re-lining to prevent groundwater contamination.
In corrosive environments concrete is prone to deterioration, particularly in alkaline soils. The concrete surface is rough making it hard to clean and the air pockets provide cavities for vegetation growth.
Lipumax-G grease traps are manufactured from glass reinforced plastic. The material is a strong yet lightweight for easy installation. The smooth surface is easy to clean and corrosion resistant.
Glass reinforced concrete is a mixture of cement, fine aggregate, chemical admixtures, glass fibres and water. The material is lightweight but is brittle, prone to cracking and porous.
Glass reinforced concrete grease traps require regular maintenance and re-lining to prevent groundwater contamination. In aggressive environments the material is prone to deterioration, particularly in alkaline soils.
The Australian Standard, AS 4494: Discharge of commercial and industrial liquid waste to sewer, states that the receiving water authority has the power to regulate the use and design of grease traps in their jurisdiction.
Local water authorities have specific regional requirements. They recommend the size of the grease trap, the total volume of wastewater to be held in retention and approve the installation of the grease trap.
To ensure the longevity of the installation, water authorities usually provide a conservative estimate for the volume of wastewater to be treated.
For the latest water authority requirements, visit approved product markets page.
ACO’s range of grease traps are designed and manufactured in Europe in accordance with EN 1825: Grease traps. ACO Australia believes that this is the most appropriate internationally recognised performance based standard.
EN 1825 specifies a wastewater quality requirement of a maximum 25mg/L concentration of hydrocarbons. This ensures that a grease trap can effectively separate Fats, Oils and Grease (FOG) from wastewater, before discharging it into the sewer system.
Install the grease trap as close as possible to the source of the grease to minimise the sediment build-up in long runs of pipe. However, to ensure food hygiene standards are maintained, grease traps should not be installed in close proximity to food preparation areas in kitchens and processing facilities.
Position the grease trap in a location that enables waste management vehicles to easily access and service the trap. Prior to the installation, contact the grease removal contractor to obtain a written agreement that the grease trap is serviceable.
Lipumax below ground grease traps require trafficable covers to enable access for maintenance. The access covers must comply with specific load class regulations.
Load Class Standards are recommendations only and there are a number of other factors to consider when selecting the grease trap.
Type of traffic – The weight of loads trafficking the grease trap, for example forklifts, trolleys and maintenance trucks.
Wheel type – Solid tyres exert more stress than pneumatic tyres and heavily loaded trolleys can also intensify the load, requiring a heavy duty access cover.
Frequency and speed of traffic – Frequent and fast traffic can intensify the load.
Position of cover – If the access cover is positioned at the bottom of a ramp or where traffic will be turning and/or braking, the cover will be subjected to extreme forces.
Lipumax below ground grease traps are available with a choice of AS 3996 Load Class B and D compliant gas and water tight access covers. The covers are encased in precast concrete collars.
For Class D applications, ACO offers an optional reinforced concrete load distribution plate to help distribute the applied load. A riser tube is also available to protect the pipework from excessive load stress. For structurally designed reinforced slabs and pavements, the riser tube and precast load distribution plate can be omitted. For more information, see installation guide.
Below ground grease traps require a removable cover for access and maintenance purposes. Grease trap with multi-part access covers are cumbersome, costly and time consuming to install and are difficult to access for maintenance.
Lipumax is designed with a single access point for quick and easy maintenance. ACO has a choice of access covers and reinforced precast concrete collars.
ACO in Australia has been supplying the market with access covers for over 15 years and has experience in providing solutions for a wide range of applications.
ACO has gained NATA accreditation (No. 15193) for its testing laboratory and can provide NATA certified test reports for load tests carried out to AS 3996.
ACO’s Lipumax grease traps are specifically designed for below ground installations and are engineered with features to help prevent buoyancy.
Buoyancy is described as the upward force exerted by fluids and weight (gravity) is the downward force produced by an object. A body’s ability to key in to the surrounding soil produces friction which in turn also acts to resist buoyancy. Buoyancy exits in soils where there is a high water table and has the potential to cause an installed grease trap body to float.
The Lipumax body features ribs to key into the surrounding material and allows for soil to be compacted around and above the body. The precast concrete collar adds weight that acts as an anchor to prevent uplift.
If buoyancy is a concern, ACO recommends using the load distribution plate and / or cast in situ concrete encasement to provide additional weight to the trap body.
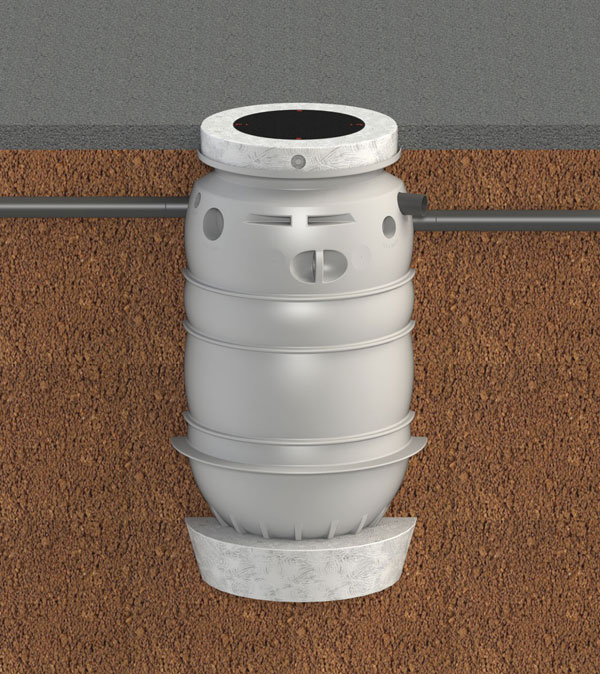
Buoyancy must be addressed when installing below ground grease traps in high water tables.

In high water table environments, weight must be added to the structure by a load distribution plate and / or concrete encasement.